Кузнечно-прессовое оборудование. Кузнечно-прессовое и термическое оборудование
Обработка и формовка металлов, включающая кузнечные процессы, гибку, сварку, резку, и другие операции, невозможна без использования кузнечно-прессового оборудования, которое необходимо не только для изготовления конкретных кованых объектов, но и для производства металлических заготовок – они будут вовлечены в дальнейший производственный цикл. Принцип действия кузнечно-прессового оборудования основан на формовании металла под давлением, что является сложным и трудоемким процессом, и на пластической обработки первоначальных заготовок. Оба этих процесса в качестве своеобразного побочного эффекта делают металл более плотным, прочным, устойчивым к механическим и температурным воздействиям. Кузнечно-прессовое оборудование бывает механическим и автоматическим – в зависимости от способа действия и типа управления. Также подобное оборудование классифицируется в соответствии с итоговым продуктом: оборудование для обработки материала (заготовок) и для финишной формовки изделий. Выбор конкретного кузнечно-прессового аппарата происходит в зависимости от масштабов производства, от необходимой производительности и видов выполняемых операций.
Штамповочный пресс предназначен для обработки металла давлением. Штамповка может быть холодной и горячей, и штамповочный пресс производит именно холодную штамповку – листовую и объемную. Это высокоточный процесс, характеризующийся высокой производительностью, в процессе которого исходный материал подвергается значительной пластической деформации, что нужно учитывать при выборе исходного материала. При листовой штамповке получается прокатный лист (лента) различной толщины – от сотых миллиметра до нескольких сантиметров, в зависимости от назначения. Продукция, изготавливаемая при помощи штамповочного пресса, крайне широко используется в сфере обработки металлов – в том числе в качестве промежуточного материала.
Гибочный станок используется для гибки листа (листогибочные), профиля, труб и других металлоизделий под определенным углом. Весь ассортимент гибочных станков широко применяется во всех сферах строительства и производства, как для стационарных работ в заводских условиях, так и для выездных работ «на объекте». По принципу действия гибочные станки делятся на пневматические (используют воздух и работу компрессора), электромагнитные (используют силу промышленного магнита), электромеханические и мобильные. В соответствии с видом итоговой продукции гибочные станки бывают узкопрофильными – к ним относится такое оборудование, как листогибы (используются для гибки металлического листа и профиля, бывают гидравлическим и ручным), профилегибочные станки (используются для гибки профиля, бывают механическими, гидравлическими и универсальными), кромкозагибочные станки (используются для загиба краев) и т.д. Также гибочные станки могут быть универсальным оборудованием, работающим и с листовым металлом, и с трубами, и с профилем.
Кузнечный молот (пневматический) – это ударный кузнечно-штамповочный станок, чье действие обусловлено накопленной кинетической энергией. То есть кинетическая энергия преобразуется в ударную массу; пневматическая конструкция установки позволяет обойтись наименьшими энергозатратами и минимизировать тяжелый ручной труд. Главной характеристикой каждого конкретного молота является масса падающей части (рабочего молота), причем вариантов много – от 50 до 1000 кг в среднем. Другим показателем этого оборудования считается эффективная кинетическая энергия (накопленная к моменту удара энергия). Хороший молот имеет удобную систему регулировки, возможность точной настройки, работы над заготовкой с нескольких сторон.
Гильотины (гильотинные ножницы) являются вспомогательным, но необходимым оборудованием по отношению к процессам ковки. Этот вид оборудования используются для резки всех видов металла, а так как резка является обязательным элементов в любом металлообрабатывающем процессе, то гильотины и гильотинные ножницы применяются во всех смежных областях – от машиностроения и самолетостроения до мелкого производства металлоизделий. Гильотины и гильотинные ножницы различаются по принципу действия и бывают ручными, электромеханическими и пневматическими; выбор конкретного вида гильотины зависит от объема и типа производства. Основными характеристиками гильотин являются длина реза и максимальная толщина, эти показатели также учитываются при выборе и выбираются в зависимости от того, с какими заготовками в процессе изготовления предстоит работать.
В целом, играющее в процессе изготовления кованых изделий центральную роль, кузнечно-прессовое оборудование требует тщательного выбора при покупке – так же, как и прочее металлообрабатывающее оборудование. При выборе кузнечно-прессового оборудования опираются на следующие факторы: во-первых, объемы производства; во-вторых, необходимая точность обработки; в-третьих, используемые при производстве материалы и заготовки в общем; в-четвертых, оснащенность производства (в частности, от этого зависит выбор между электромеханическими, пневматическими и ручными станками). Кроме того, важно заранее продумать перспективы развития производства и расширения ассортимента – для того, чтобы приобретенное оборудование было адекватным плану развития, иначе уже через год или даже меньше вам придется приобретать новые, более производительные, станки. Также напомним, что качественное металлообрабатывающее оборудование, как правило, производится опытными фирмами, зарекомендовавшими себя долгими годами работы и логичным рядом моделей, а также имеет все сертификаты соответствия. При покупке для предприятия сразу нескольких станков, относящихся к одному типу выполняемых функций, рекомендуется приобретать оборудование одной фирмы – это будет способствовать цельности производства, и желательного у одного Поставщика.
Выбор КПО чрезвычайно велик. В зависимости от объема работы, который должен выполняться, подбирается оборудование. Лучше всего, подбирать оборудование, которое максимально подходит для потребностей предприятия. Перед выбором оборудования, предварительно проконсультируйтесь со специалистом в данном направлении.
Кузнечно-прессовое оборудование представляет собой класс станков и аргегатов в достаточно широком ассортименте – от многофункционального до специфического оборудования. Кузнечно-прессовые станки различаются габаритами, интенсивностью использования, наличием автоматического и компьютерного управления либо полуавтомата, количеством функций, точностью, универсальностью.
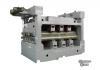
История таких инструментов, как кузнечное оборудование, начинается еще с тех времен, когда для ковки использовались молоты, горны, клещи и наковальни. Но прошли годы совершенствования, и сегодня корпорация «Станкоснаб» готова предложить покупателям инновационные электронные станки, работающие под минимальным контролем со стороны оператора. Применение в работе такого современного кузнечно-прессового оборудования приводит к:
- снижению временных затрат на изготовление той или иной продукции,
- снижению себестоимости каждой изготовленной детали,
- увеличению конкурентоспособности продукции на рынке.
Разнообразие модификаций кузнечно-прессового оборудования
Кузнечное оборудование, представленное в нашем каталоге товаров, гарантированно обеспечит получение заготовок заданной формы при соблюдении высокого качества изделий. Поэтому детали, изготовленные на таких станках, будут обладать высокой прочностью, способностью выдерживать повышенные нагрузки и надежностью.
Прибегнув к услугам корпорации «Станкоснаб», каждый покупатель сможет приобрести по доступной цене и с максимальным удобством для себя такое прессовое оборудование как:
- гильотинные ножницы,
- прессы,
- линии, предназначенные для раскроя листов металла,
- молоты,
- листогибочные машины и прессы,
- листоправильные устройства,
- вальцы (трехвалковые и четырехвалковые машины),
- кузнечно-прессовые автоматы,
- комбинированные пресс-ножницы.
Все это прессовое оборудование отличается между собой как конструкцией, так и принципом действия. В зависимости от этого, данные устройства делятся на пять групп:
- молоты,
- прессы,
- ротационное оборудование,
- кузнечно-прессовое оборудование,
- импульсные установки,
- станки статического действия.
То есть в данную категорию попадет не только кузнечное оборудование, но и множество иных машин, которые будут использоваться в разнообразных технологических процессах. Это и различные металлообрабатывающие операции, проводимые при холодной штамповке, в том числе и объемной. Данные станки станут оптимальным вариантом не только при оснащении цехов масштабных промышленных предприятий, но и при подборе оборудования для небольших производств.
Современное кузнечно-прессовое оборудование – первый шаг к модернизации производства
Современное кузнечное оборудование, представленное в каталоге наших товаров, позволит организовать на любом предприятии замкнутый рабочий цикл. Он будет включать в себя все операции, начиная от черновой обработки заготовок и заканчивая выпуском изделия, полностью готового к продаже или последующему применению.
Одним из основных достоинств, которыми обладает кузнечно-прессовое оборудование, является возможность оперативно получать заготовки, чрезвычайно близкие по своим параметрам к конфигурации и размерам готового изделия. Поэтому их доработка – это оперативный процесс, требующий минимальных временных и трудовых затрат. А в ряде случаев дополнительная обработка может просто не понадобиться. Так же применение прессового оборудования сводит к минимуму:
- металлические отходы,
- потребление электроэнергии,
- затраты рабочей силы.
Обратившись в компанию «Станкоснаб», вы сможете не только приобрести кузнечное-прессовое оборудование, способное механизировать трудоемкие процессы, связанные с обработкой металлов. Вы совершите первый уверенный шаг к модернизации собственного производства, заменив старые и несовершенные станки новым инновационным оборудованием. В каталоге товаров в широком ассортименте представлено разнообразное кузнечное и прессовое оборудование, отличающееся мощностными показателями. Поэтому каждый покупатель той или иной продукции сможет легко подыскать для себя станки, соответствующие его производственным потребностям, а так же финансовым возможностям.
Подобрать оптимальный вариант оборудования, вам помогут опытные консультанты. Они не только ответят на любые интересующие вопросы, но и помогут сделать оптимальный выбор. Наше оборудование – это гарантия качества, высокий уровень сервиса и привлекательные цены.
Отправить свою хорошую работу в базу знаний просто. Используйте форму, расположенную ниже
Студенты, аспиранты, молодые ученые, использующие базу знаний в своей учебе и работе, будут вам очень благодарны.
Размещено на http://www.allbest.ru/
Министерство образования и науки РТ
ГАОУ СПО «Бугульминский машиностроительный техникум»
Доклад по теме:
«Кузнечно-прессовое оборудование»
Выполнил:
Студент 4 курса
949 группы БМТ
Гумеров Р.И.
Проверил
Преподаватель:
Аминов И.Р.
Описание
Классификация
Предназначение
кузнечные ножницы пресс молот зигмашина
Описание кузнечно-прессо вого оборудования
В сфере металлообработки очень широко востребовано кузнечно-прессовое оборудование, которое используется для выполнения различных операций и совершенно необходимо при изготовлении изделий из металла, а также и в других областях производства.
Кузнечно-прессовое оборудование включает в себя гильотинные ножницы, пресс-ножницы, прессы кривошипные, гидравлические прессы, листогибочные машины, прессы механические, листогибы, листогибочные машины, листогибочные прессы, молоты, зигмашины, прессы для пакетирования металлических отходов и прессы для пакетирования бумаги и отходов.
Среди наиболее популярных станков этого типа можно отметить гильотинные ножницы, листогибы и листогибочные прессы, гидравлические прессы и молоты. Гильотинные ножницы используются для резки и раскроя листового металла. Существуют ручные, пневматические, механические, гидравлические, гильотины с ЧПУ или автоматические гильотинные ножницы, и их комбинации.
Листогиб представляет собой оборудование для гибки металла путем прокатывания металлического листа между вальцами для придания ему нужной формы изгиба. Этот процесс может быть одно- и многопроходным, разнообразие листогибов позволяет изготавливать изделия разной формы. Прессы листогибочные предназначены для загиба, штамповки и рихтовки листового металла.
Пресс гидравлический используется для холодной штамповки металла, а также прессования отходов. Благодаря гидравлическому приводу становится возможным получать большое давление, прилагая малое усилие, вот в чем причина популярности этого оборудования.
Молот - машина ударного действия для пластической деформации металлических заготовок, это один из основных станков кузнечно-штамповочного производства. Молот используется для ковки и объёмной и листовой штамповки. По типу привода выделяют паровоздушные, пневматические, гидравлические, высокоскоростные газовые, взрывные, приводные механические и электромагнитные молоты.
Классификация кузнечно-прессового оборудования
В зависимости от характера воздействия рабочих органов на заготовку в процессе деформирования металла и устройства механизмов для привода этих органов кузнечно-прессовое оборудование подразделяют на молоты, прессы, горизонтально-ковочные и специальные машины.
Молотами называются кузнечные машины, на которых обработку металла осуществляют ударами падающих частей. Деформирование металла на молотах происходит в условиях динамического приложения нагрузки. В начале деформирования (момент соприкосновения с заготовкой) падающие части имеют максимальную скорость, доходящую до 9 м/с. После окончания деформирования металла скорость падающих частей равна нулю.
По принципу действия молоты подразделяют на молоты простого и двойного действия.
В молотах простого действия энергия удара создается только падающими частями, подъем которых осуществляют с помощью пара, сжатого воздуха или какого-либо другого энергоносителя. В молотах двойного действия энергия удара создается падающими частями при одновременном дополнительном воздействии на них каким-либо энергоносителем. Падающие части этих молотов не просто поднимаются вверх и падают, а для усиления ударов еще принудительно разгоняются действием пара, сжатого воздуха и другими способами, что увеличивает скорость их падения.
В настоящее время молоты простого действия применяют ограниченно. Молоты двойного действия по сравнению с молотами простого действия при одной и той же массе падающих частей обладают большей кинетической энергией.
По конструкции молоты различны. По типу привода их подразделяют на паровоздушные, пневматические, механические, гидравлические, газовые и высокоскоростные.
Паровоздушные молоты приводятся в действие паром или сжатым воздухом, вырабатываемым соответственно в паровых котлах или компрессорных установках. Пар или сжатый воздух поступает по трубопроводам в рабочий цилиндр молота и, действуя на поршень, осуществляет подъем и разгон падающих частей молота. Нанося удар по заготовке, подвижные части осуществляют деформирование металла.
Пневматические молоты приводятся в действие сжатым воздухом, поступающим в рабочий цилиндр от компрессорного цилиндра, встроенного в машину.
В отличие от паровоздушных молотов в пневматических молотах воздух выполняет роль как бы пружины, связывающей рабочий и компрессорный поршни молота. Компрессорный поршень приводится в движение от кривошипного вала и при движении поршня вверх воздух над ним сжимается и поступает в рабочий цилиндр, где он давит на рабочий поршень, заставляет его двигаться вниз, разгоняя падающие части молота, которые наносят удар по заготовке.
После нанесения удара в пневматических молотах простого действия падающие части поднимаются вверх благодаря разряжению, которое образуется в рабочем цилиндре при движении компрессорного поршня вниз. В молотах двойного действия падающие части поднимаются сжатым воздухом, который из компрессорного цилиндра поступает под поршень рабочего цилиндра при движении компрессорного поршня вниз.
Механические молоты для передачи движения от электродвигателя к падающим частям снабжены механизмами, обязательной частью которых является жесткая, гибкая или упругая связь. Например, в молотах с гибкой связью падающие части поднимаются вверх цепью, канатом или ремнем, которые наматываются на ролик.
Гидравлические молоты приводятся в движение жидкостью высокого давления, которая воздействует на плунжер, связанный с падающими частями молота.
Газовые молоты приводятся в движение энергией газов, образующихся при сгорании топлива, впрыскиваемого в рабочий цилиндр молота.
Высокоскоростные молоты приводятся энергией газов, сжимаемых с помощью гидравлических устройств.
Наиболее широкое применение в кузнечном производстве получили паровоздушные и пневматические молоты двойного действия.
Отечественной промышленностью выпускаются паровоздушные молоты с номинальной массой падающих частей от 1 до 7,25 т, пневматические молоты с массой от 50 до 1000 кг. В номинальную массу падающих частей входит масса бабы, штока, поршня и верхнего бойка. Паровоздушные молоты являются универсальными машинами и используются как для свободной ковки, так и для штамповки. Пневматические молоты в основном используются для свободной ковки и реже для штамповки.
Ковочные прессы подразделяют на гидравлические, механические, паро- и воздушно-гидравлические.
Гидравлические прессы по сравнению с молотами деформируют металл заготовки с меньшими скоростями. Скорость движения инструмента у гидравлических прессов не превышает 0,3 м/с. Основную работу по деформированию металла они совершают не за счет массы и скорости движения падающих частей, а за счет давления жидкости, развиваемого в рабочих цилиндрах. В настоящее время в гидравлических прессах создают давление жидкости до 98 МПа, а наиболее крупные прессы развивают усилие до 685 МПа. Механические прессы осуществляют деформацию металла инструментом, приводимым в движение с помощью различных механизмов, преобразующих вращательное движение электродвигателя в возвратно-поступательное движение инструмента. Наиболее распространены кривошипно-шатунные, рычажные, реечные и винтовые механизмы.
Механические прессы отличаются от гидравлических прессов и молотов тем, что у них имеется жесткая связь через систему механических передач между инструментом и электродвигателем. Однако в процессе деформирования металла основную работу производит не электродвигатель, а элемент пресса (маховик), обладающий большим моментом инерции. После пуска электродвигателя пресса маховик разгоняется и вращается с определенной максимальной частотой, запасая значительную энергию. В процессе рабочего хода инструмент соединяется с маховиком, и он отдает часть запасенной энергии на деформацию металла заготовки. Частота вращения маховика при этом обычно снижается не более чем на 20%. После окончания рабочего хода электродвигатель снова разгоняет маховик до определенной максимальной частоты вращения.
Выбирают ковочные молоты и прессы согласно эмпирическим формулам, диаграммам или таблицам. Пневматические ковочные молоты используют для производства поковок небольшой массы из заготовок сортового проката, а также для протяжки длинных заготовок, ковки запасных частей, заготовок для инструмента и ремонтных операциях.
Предназначение кузнечно-прессового оборудования
Кузнечно-прессовое оборудование, предназначено для обработки металла давлением. В принципе, обработка металла давлением, это достаточно трудоёмкий технологический процесс, который можно осуществить только при помощи специального оборудования. Обработка металлов кузнечно-прессовым оборудованием, имеет высокую производительность и низкую энергоемкость, кроме этого, благодаря обработке давлением, экономится значительная часть металла. После обработки кузнечно-прессовым оборудованием, металл становится более плотным, увеличиваются его механические свойства.
Благодаря кузнечно-прессовому оборудованию, можно обрабатывать любой металл. Пластическая обработка металла, так же производится с помощью кузнечно-прессового оборудования. В результате пластической обработки (горячей или холодной), улучшаются свойства металла.
Прессование металла, имеет множество преимуществ, например возможность успешной пластической обработки металлов и сплавов, а так же получение практически любого поперечного сечения (при других способах обработки металла, это получается не всегда), кроме этого, изделия, обработанные с помощью кузнечно-прессового оборудования, имеют высокое качество.
Способов обработки металлов давлением, очень много, но особое место в этом списке, занимает обработка холодноштамповочным оборудованием. Холодная штамповка имеет массу особенностей, а именно: изготовление сложных изделий с высокой точностью, высокая производительность, небольшая энергоемкость и др.
Благодаря листовой штамповке, можно получить жесткие, прочные и в тоже время легкие изделия из минимального количества исходного материала. Листовую штамповку для кузнечно-прессового оборудования, широко применяют в разных отраслях промышленности. Листовая штамповка - это обработка давлением исходной заготовки в виде полосы, ленты или листа. Операции, которые производятся при помощи оборудования для холодной листовой штамповки, разделяют на две группы: формоизменяющие и разделительные. С помощью этого оборудования, можно производить следующие операции: отрезку, вырубку, пробивку, вытяжку, высадку, калибровку и чеканку металла.
Размещено на Allbest.ru
...Подобные документы
Особенности кузнечно-прессового оборудования, влияющие на выбор способа контроля. Принцип действия электроконтактного устройства для контроля. Фотоэлектрические, радиоволновые и радиоизотопные средства контроля в кузнечно-штамповочном производстве.
реферат , добавлен 16.07.2015
Загрузочные устройства для мелких заготовок. Принцип работы и классификация оборудования для удаления штампованных изделий и отходов. Технологические предпосылки механизации кузнечно-штамповочного производства. Показатели для расчетов его эффективности.
контрольная работа , добавлен 16.07.2015
Изготовление уникального высокопроизводительного проката, металлургического, кузнечно-прессового, гидротехнического, горнорудного оборудования. Формовка крупных отливок. Состав смесей, изготовляемых по Фуран процессу. Составы карбомидофурановых смесей.
отчет по практике , добавлен 04.06.2011
Определение закона движения механизма. Кинестетический силовой расчет основного рычажного механизма. Проектирование цилиндрической эвольвентной зубчатой передачи. Построение графика углового ускорения звена приведения в функции обобщенной координаты.
курсовая работа , добавлен 05.12.2012
Проект участка кузнечно-прессового цеха для изготовления детали "втулка". Обоснование выбора кривошипного горячештамповочного пресса. Расчет усилий штамповки, численности работников цеха. Расчет и подбор технологического оборудования; схема рабочих мест.
лабораторная работа , добавлен 22.12.2015
Особенности кузнечно-штамповочного производства. Классификация технологических процессов и изделий КШП, применяемое оборудование. Виды деформации металла. Исходные заготовки для поковок, способы их разделки. Характеристики точности и металлоемкости в КШП.
презентация , добавлен 18.10.2013
Назначение и механическое оборудование цеха, организация технического обслуживания и ремонта. Назначение, устройство, кинематика и принцип действия гильотинных ножниц с нижним резом, расчет расхода смазки узла и агрегата, расчет агрегата на прочность.
курсовая работа , добавлен 06.06.2010
Структурный и кинематический анализ механизма кузнечно-штамповочного автомата методом планов и диаграмм. Определение сил и реакций, действующих на звенья в кинематических парах. Определение уравновешивающей силы методом "жесткого рычага" Н. Жуковского.
курсовая работа , добавлен 01.11.2013
Роботизированный технологический комплекс как автономно действующая автоматическая станочная система. Применение РТК в кузнечно-прессовом производстве, виды роботизированных комплексов, требования к ним. Способы крепления оборудования на фундаменте.
контрольная работа , добавлен 07.09.2012
Характеристика ремонтируемых машин. Расчет производственной программы участка, оборудования, количества рабочих мест и постов. Определение производственных площадей. Проектирование технологического процесса разборки шасси трактора Т 130, карта эскизов.
Выполняемые работы . С помощью кузнечно-прессового оборудования получают заготовки в виде поковок или штамповок, а также правят и упрочняют поверхности. Соответственно, работы, выполняемые на оборудовании этого типа, делятся на ковку, объемную или листовую штамповку и чеканку. Перед ковкой и объемной штамповкой заготовок необходим их нагрев.
Термическая обработка заготовок предполагает их нагрев, выдержку (в ряде случаев с насыщением поверхностного слоя активными средами) и охлаждение по установленному графику.
Кузнечные молоты, прессы и инструмент . Для ковки применяют различают ковочные молоты и прессы .
По виду привода кузнечные молоты делятся на пневматические, паровоздушные и механические. По принципу действия молоты бывают одинарного и двойного действия. У молотов одинарного действия подвижная часть поднимается паром, сжатым воздухом или другим энергоносителем, при этом потенциальная энергия положения подвижной части преобразуется в энергия удара при свободном падении. Такие молоты имеют ограниченное применение. У молотов двойного действия энергия удара создается за счет свободного падения подвижной части и дополнительного воздействия какого-либо энергоносителя.
Наиболее широко применяют пневматические и паровоздушные молоты. Масса падающих частей пневматических молотов составляет от 50 до 1000 кг, паровоздушных – от 0,5 до 8,0 т. Недостатки таких молотов обусловлены низким КПД (составляет иногда 3–4 %) и большими вибрационными нагрузками. Последние разрушают обычные здания и отрицательно влияют на точность прецизионных станков, расположенных рядом.
Конструкции кузнечных молотов разнообразны, но все они основаны на общем принципе, суть которого заключается в том, что энергия, необходимая для деформирования металла, передается при помощи удара.
Молот любой конструкции имеет следующие основные части (рис. 2.50):
– падающую часть, к которой относят бабу, шток, поршень и верхний рабочий боек;
– шабот – металлический стул или крупная стальная отливка, к которой крепится нижний боек, который служит опорой для обрабатываемой заготовки. Масса шабота в 10–15 раз больше массы падающей части;
– станину с фундаментной плитой. К станине крепят рабочий цилиндр, служащий для силового воздействия на падающую часть, и механизм управления;
– привод, состоящий из электродвигателя с редуктором, кривошипно-шатунного механизма и компрессорного цилиндра;
– фундамент, служащий опорой для станины и шабота, под который укладывают для смягчения удара дубовые брусья. Фундамент ковочного пресса состоит, в свою очередь, из трех частей: двух боковых пирсов, на которые опирается станина, и средней части, на которую опирается шабот.
Инструмент для ручной ковки делят на опорный, ударный (рис. 2.51), поддерживающий и измерительный.
На опорном инструменте (наковальне или шпераке) выполняются операции ручной ковки: протяжка, осадка, гибка, пробивка, прошивка, разрубка, кузнечная сварка и правка.
Наковальни изготавливают из стали 45Л массой 70–350 кг. Верхняя плоская часть называется лицом. Его твердость составляет 40–45 HRC. Конический отросток наковальни – рог – служит для гибки пустотелых поковок. В зависимости от количества отростков наковальни бывают безрогие, одно- и двурогие.
Шперак – маленькая наковальня с двумя рогами массой до 50 кг служит для ковки мелких поковок.
Ударным инструментом являются молотки и кувалды. Молотком пользуется кузнец для нанесения ударов и указания молотобойцу места нанесения удара кувалдой.
Масса молотка 0,5–2,0 кг, он изготовлен из стали У7 или У8. Молоток имеет два бойка. Один из них круглый, квадратный или восьмигранный, имеет гладкую ударную поверхность с заваленными гранями. Другой боек может быть шарообразный, заостренный с округлым ребром или тупой. Боек молотка подвергают закалке с последующим отпуском.
Кувалды – основной инструмент массой 2–16 кг для нанесения ударов по нагретой заготовке. Они также имеют два бойка и подразделяются на тупоносые и остроносые. Для закрепления рукоятки в кувалде делают овальное насадное отверстие, которое расширяется от середины к краям. Материал кувалд – стали 40, 45, 50 и У7. После термической обработки твердость рабочего слоя толщиной до 30 мм составляет 48–52 HRC.
Кузнечные зубила предназначены для горячей и холодной рубки металла. Первые затачивают на угол не менее 60 о, вторые – на угол не более 50 о. Зубила изготавливают из стали У7 или 6ХС. Лезвие зубил может быть прямым, полукруглым или фасонным. Твердость рубящей части инструмента на длине 30 мм составляет 50–56 HRC, а ударяемой части на высоту 20 мм – 30–40 HRC.
Подсечки изготавливают из стали У7. Они являются подкладными зубилами и вставляются квадратным хвостовиком в соответствующее отверстие наковальни. Лезвие подсечки твердостью 48–52 HRC может быть прямое или фасонное.
Пробойники (бородки) из стали 40, 45 или У7 применяют для пробивки круглых, квадратных, прямоугольных и других отверстий.
Обжимки служат для подкатки и отделки боковых поверхностей (цилиндрических, плоских и др.). Обжимки куют из стали 40, 45, 50, 40Х или У7 и после обработки резанием закаливают и отпускают на твердость 48–52 HRC по рабочей части и 30–40 HRC – по ударяемой.
Подбойки используют для ускорения протяжки и выделки желобов. Они могут иметь разнообразную форму рабочих поверхностей: плоскую, полукруглую и др. Подбойки делают из стали 40Х, 50Г или У7.
Гладилки предназначены для сглаживания неровностей и окончательной отделки плоских поверхностей поковок. В головке, расположенной над рабочей поверхностью, имеется отверстие для деревянной ручки. Гладилки изготавливают из стали 40, 45 или У7.
Деревянные ручки инструментов для ручной ковки изготавливают из клена, кизила, бука, рябины или молодого дуба. Запрещается их изготавливать из крупнослойных пород дерева, в том числе из ели и сосны. Конец ручки в отверстии инструмента расклинивают стальными «заершенными» клиньями. Длина клиньев не должна превышать ⅔ глубины насадного отверстия инструмента.
Гвоздильни – металлические пластины, кованные из стали 45 или У7. Они имеют отверстия для высадки головок болтов, заклепок, гвоздей и др.
Кузнечная форма – литая плита из стали 35Л или 40Л массой до 50 кг со сквозными отверстиями и фасонными вырезами на боковых поверхностях. Она предназначена для отделки поковок, пробивки отверстий и профильно-гибочных работ.
Поддерживающий инструмент – это клещи, манипулятор-кантователь и устройство для подвески.
Кузнечные измерительные инструменты – кронциркули, нутромеры, кругломеры, угломеры и шаблоны.
Ковку на прессах выполняют в открытых и закрытых штампах. В гидравлических ковочных прессах (рис. 2.52) энергию подвижной части передают при помощи жидкости под высоким давлением. Возникающие в процессе работы молота силы замыкаются в станине и на фундамент не передаются. Недостатки гидравлических прессов обусловлены их тихоходностью и сложностью конструкции. В кузнечных цехах машиностроительных заводов распространены ковочные гидравлические прессы с усилием 20000–30000 кН.
Гидравлические, кривошипные и фрикционные прессы . Гидравлические прессы служат для сборки (запрессовывания), прошивки, правки, гибки, развальцовки, просечки и других работ. Прессы могут быть одно- и двухстоечными. Главный параметр прессов – номинальное усилие. В производстве широко применяют прессы с усилием 40–2500 кН (ПБ6316А – 40 кН, П6326 – 400 кН, П6328 – 630 кН, ПБ6330 – 1000 кН, П6332Б – 1600 кН, ПБ6334А – 2500 кН).
Сварная станина одностоечного пресса имеет С-образную форму (рис. 2.53). В верхней части станины имеется плита с отверстиями для установки цилиндра, на нижней консольной части крепится стол или запрессовочная плита.
Приводной цилиндр установлен в верхней части станины. Шток цилиндра приводится от насосов поршневого (высокого давления) или шестеренчатого (низкого давления). Цилиндр и шток стальные, поршень и втулка чугунные. Механизм управления прессом состоит из педали, рукоятки, системы рычагов с пружинами и устройством для автоматического останова. Ход штока вверх и вниз ограничен регулировкой подвижных кулачков.
Запрессовочная оснастка состоит из подушки, прикрепленной к штоку цилиндра, и чугунной плиты с проемом для установки деталей. Плита крепится на нижней части станины. По специальному заказу прессы поставляются с правильным столом.
Пресс управляется рукояткой и педалью, связанными между собой.
Кривошипные механические прессы (рис. 2.54) служат для листовой штамповки. Основные работы – вырубка, пробивки и гибка. Применяют пресса однокривошипные открытые простого действия усилием 100, 160, 250, 400, и 630 кН.
Фрикционные прессы (рис. 2.55) имеют в приводе фрикционную передачу, которая позволяет остановку ползуна в различных нижних мертвых точках, что исключает заклинивание пресса при использовании закрытых штампов. Прессы предназначены для холодной и горячей объемной штамповки, чеканки и других целей. Из-за низких производительности и КПД фрикционные прессы имеют ограниченное применение.
Оборудование для ремонта кузовов включает измерительные системы (механические и электронные) и стапели. С помощью измерительных систем (рис. 2.56) устанавливают факт изменения тестовых размеров кузова (например, при аварии автомобиля), установленных заводом-изготовителем. Стапели (рамные, платформенные и рельсовые) служат для закрепления кузова и приложения разнонаправленных сил для его правки. Рамный стапель состоит из эстакады с трапом и рельсовыми опорами, к которым с помощью специальных захватов крепится автомобиль (рис. 2.57). Платформенный стапель содержит въездную подъемную платформу (рис. 2.58). Рельсовый стапель состоит из вмонтированных в пол рельсов, стоек и креплений (рис. 2.59). Деформированные участки кузова вытягивают пневмогидравлическим приводом с цепями.
Особенности нагрева заготовок . Заготовки нагревают перед обработкой давлением и при термической обработке (отжиге, закалке, отпуске).
Рациональный режим нагрева заготовок обеспечивает максимально возможную скорость нагрева материала без трещин из-за термических напряжений. Последние возникают в связи с тем, что внешние слои заготовки прогреваются раньше внутренних и расширяются больше. При этом внутренние слои сдерживают расширение внешних слоев. В связи с этим в сильно нагретых слоях возникают сжимающие напряжения, а в малопрогретых слоях – растягивающие напряжения. Если при недостаточной пластичности металла растягивающие напряжения достигают предела прочности металла, то последний начнет разрушаться. Если металл обладает высокой пластичностью, то термические напряжения приведут к пластическому деформированию металла и разрушения не произойдет.
С повышением температуры нагрева возрастает пластичность металла, а опасность появления трещин исчезает до того, как металл нагреется до температуры структурных превращений. Другим не менее важным условием является то, чтобы до начала ковки металл был равномерно прогрет по всему сечению слитка или заготовки.
Заготовки диаметром или стороной квадрата менее 100 мм из конструкционных или низколегированных сталей загружают в горячие печи, рабочее пространство которых имеет температуру на 100–150 °С более высокую, чем требуемая конечная температура нагрева металла. Скорость нагрева их не ограничивают. Заготовки из высоколегированных, низкопластичных сталей сначала нагревают медленно до температуры 650–850 °С, а затем быстро до ковочной температуры. Нагрев до температуры ковки уменьшает в 10–15 раз сопротивление деформированию по сравнению с процессом в холодном состоянии. Нагрев заготовок из углеродистых сталей до 350 °С не увеличивает, а снижает пластичность, а нагрев свыше 700 °С приводит к появлению окалины. Поэтому нагрев таких заготовок целесообразен в указанном отрезке температуры.
Термическое оборудование . Кузнечный горн – простейшее нагревательное устройство, в котором заготовка непосредственно соприкасается с продуктами горения топлива (рис. 2.60). Его применяют при нагреве небольших заготовок при ручной ковке. Горны бывают переносными и стационарными. Первые могут применяться в полевых условиях. По способу подачи воздуха, необходимого для горения топлива, различают горны с боковым соплом и с центральной фурмой, а по количеству очагов – одно- и двухогневые. Очаг горения может быть открытым и или закрытым.
Горны имеют сварную или литую станину. В верхней части станины имеется выемка, выложенная огнеупорным кирпичом. На дне выемки установлена фурма, через которую вентилятором подают воздух под давлением 150–2000 мм вод. ст. С фронтальной стороны стол имеет бачок с водой для охлаждения инструмента. Дымовые газы удаляются из горна через зонт и вытяжную трубу.
В качестве топлива для горнов используют коксующиеся сорта углей, кокс и редко древесный уголь. При производительности открытого горна 80–120 кг нагретого металла в час расход топлива составляет 25–50 кг/ч. Кпд такого горна составляет 2–5 %. Стационарные закрытые горны имеют более высокую производительность и большую экономичность.
Преимущества горнов – простота конструкции и эксплуатации. Недостатками являются низкая производительность, малый кпд, неравномерный нагрев заготовок, повышенный угар и насыщение поверхностных слоев металла серой из топлива.
Кузнечно-прессовые и ремонтные цеха, в которых выполняются операции ковки, штамповки при средне- и мелкосерийном типе производства, оснащают газовыми кузнечными печами (рис. 2.61).
Оборудование для термической обработки делят на основное и вспомогательное.
К основному оборудованию относят нагревательные печи, печи-ванны, закалочные баки, с помощью которых выполняют основные операции термической обработки. Это оборудование различают по:
– широте выполняемых функций: универсальное и специальное;
– значению температуры: низко-, средне- и высокотемпературное;
– тепловому источнику: твердотопливное, мазутное, газовое, электрическое, индукционное;
– конструктивным признакам: камерное, шахтное, щелевое, очковое, с выдвижным подом, элеваторное, со съемным сводом, толкательное, конвейерное и др.;
– характеру загрузки и выгрузки заготовок, периодичности и непрерывности загрузки: с периодической и непрерывной загрузкой. В печах первого вида заготовки загружаются и выгружаются через одно окно, а в процессе обработки остаются неподвижными. В каждый момент времени температура во всей зоне нагрева заготовок одинакова. В печах второго вида, называемых методическими, заготовки во время обработки перемещаются от окна загрузки к окну выдачи. Температура рабочего пространства в таких печах повышается от места загрузки заготовок к месту их выдачи;
– способу использования тепла отходящих газов для предварительного подогрева воздуха, поступающего в печь: рекуперативные и регенеративные.
Условное обозначение термических печей содержит буквы и числа. Буквы определяют вид нагрева, тип печи, среду и агрегатность (таблица 2.23), а цифры – активные размеры рабочего пространства (ширину, длину, высоту или диаметр и высоту) в дециметрах в числителе и максимальную рабочую температуру в сотнях градусов Цельсия в знаменателе.
Например, обозначение СНЗА-5,0.10.3,2/10 означает – агрегат сопротивления (электрический), камерный, с защитной атмосферой, размерами печного пространства 500´1000´320 мм и рабочей температурой до 1000 °С.
Таблица 2.23
Буквенное обозначение печей для термической обработки
Первая буква | Вторая буква | Третья буква | Четвертая буква | ||||
Обозначение | Вид нагрева | Обозначение | Основной конструктивный признак | Обозначение | Характер среды | Обозначение | Отдельные особенности |
Г С И Т | Газовый Сопротивление Индукционный Пламенный | А Б В Г Д Е И К Н П Р Т Ш Э | Карусельная Барабанная Ванна Колпаковая Выдвижной под Подвесной конвейер Пульсирующий под Конвейерная Камерная Протяжная Рольганговая Толкательная Шахтная Элеваторная | А В Г З М О П С Ц | Азот Вакуум Металлы Защитная атмосфера Масло Окислительная атмосфера Пар водяной-вода Соль (селитра) Цементационный газ | А Л В М Н П | Агрегат Лабораторная Вертикальная Механизированная Непрерывного действия Периодического действия |
Для отпуска, отжига и закалки, например, используют электропечи СТО, СТЗ, СКЗА, универсальные камерные электропечи СНО, СНЗ, шахтные электропечи СШО, СШЗ, вакуумные СШВ, электрованны СВГ, СВС. Для химико-термической обработки широко используют шахтные безмуфельные электропечи, для газовой цементации – СШЦ, для газового азотирования – США. Для индукционного нагрева применяют специальные генераторы и установки.
Внешний вид нагревательных печей с различными конструктивными признаками приведен на рисунках 2.62–2.64.
К вспомогательному оборудованию относят правильные прессы, машины для очистки деталей и др.
Термическое оборудование должно обеспечить следующие требования:
– обеспечить экономичный нагрев до заданной температуры за минимальное время;
– при заданной длительности нагрева угар и обезуглероживание не должны превышать допустимых норм;
– процессы, связанные с нагревом и обслуживанием печей, должны быть максимально механизированы или автоматизированы;
– работа печей не должна оказывать вредного воздействия на человека и окружающую среду.
Для контроля работы термического оборудования применяют различные приборы. Температуру рабочего пространства и нагреваемого металла измеряют пирометрами, которые по принципу действия могут быть оптическими, термоэлектрическими, радиационными и фотоэлектрическими. Давление выше атмосферного измеряют манометрами, а ниже атмосферного – вакуумметрами или тягомерами. Расход воздуха и топлива измеряют расходомерами. Качественный и количественный расход газов и продуктов сгорания топлива определяют газоанализаторами.
Машины для выполнения ковочно-штамповочных операций (так вернее, ибо какое-либо оборудование обычно создаётся под разработанную технологию, а не наоборот) – распространённый вид устройств для металлообработки.
Например, на машино- и приборостроительных предприятиях или заводах по производству металлоконструкций на каждые 5 металлорежущих станков обязательно приходится одна единица оборудования для обработки давлением. Причём не только металлов: например, те же ПЭТ-бутылки производятся на термопластавтоматах, которые тоже представляют специализированное штамповочное оборудование.
Всё многообразие конструкций и схем кузнечно-штамповочного оборудования (КШО) классифицируют по следующим показателям:
По температуре обрабатываемой заготовки
Машины для ковки, горячей штамповки, холодной листовой штамповки, холодной объёмной штамповки.
По виду операций, которые выполняются на машине
Различают заготовительное, основное КШО, а также КШО для заключительных стадий обработки давлением.
По способу подачи и удаления изделий из зоны обработки
Неавтоматизированное оборудование, штамповочные комплексы, машины-автоматы, автоматизированные штамповочные линии.
По типу энергоносителя
В качестве которого может использоваться электроэнергия, сжатый воздух, пар, жидкость высокого давления, а также несколько указанных источников одновременно.
По характеру обработки металла
Выделяют машины статического и динамического действия. Сюда же принято относить и установки для высокоэнергетической штамповки.
По основному технологическому параметру
Которым может быть номинальное усилие (для механических прессов), предельное усилие (для гидравлических и пневматических прессов), крутящий момент (для машин ротационного действия), энергия удара (для молотов).
Все остальные классификационные признаки – последовательность размещения основных узлов
Способ управления и т.д. — носят вспомогательный характер
Следует отметить: в вопросах названия определённых типов КШО элемент терминологической путаницы вносят различия в обозначениях технологических процессов, которые исторически приняты в отечественной и иностранной профильной литературе.
Так, машины для холодной объёмной штамповки часто именуют оборудованием для холодной ковки металла . Происходит это из-за буквального перевода английского термина cold forging (холодная ковка), который некритично воспринимается производителями КШО, в частности, из Китая, Тайваня и т.д.
Аналогично случилось и с термином forging (в иностранной литературе понятие hot forging практически не употребляется: всё, что не делает cold forging, автоматически зачисляется в горячештамповочное оборудование). Таким образом, следует точно различать принципиальные различия в областях применения КШО у нас в стране, и за рубежом, и использовать их в дальнейшем:
Оборудование для ковки
Ковка, как операция горячей обработки штучных заготовок давлением, отличается от горячей штамповки тем, что в последнем случае для формоизменения металла обязательно нужна технологическая оснастка – штамп. Чисто ковочное КШО предназначается для заготовительных операций – чаще осадки, расплющивания, открытой прошивки – а потому не содержит повышенных требований к точности полуфабриката (который в дальнейшем ещё будет обрабатываться различными способами, в том числе, и штамповкой). Поэтому оно должно обеспечивать лишь необходимую мощность формоизменения.
Для горячей ковки металла
Применяются два различных вида КШО: ковочные молоты (см. рис. 1) и гидравлические прессы (см. рис.3). Крупные ковочные молоты могут использовать в качестве энергоносителя пар и сжатый воздух, мелкие – только сжатый воздух (см. рис.2). Гораздо реже используются газовые и гидравлические молоты. Молоты имеют преимущественно вертикальную компоновку.
Рисунок 1 – ковочный паровоздушный молот
Поскольку при ковке создаются большие динамические нагрузки, то фундамент ковочного молота с подштамповой плитой обычно отделяется от остальных его узлов, что хорошо заметно на рис.1.
Рисунок 2 – Пневматический ковочный молот.
Молоты
Для свободной ковки отечественного производства маркируются буквой М/МА и четырьмя цифрами, две первых определяют тип энергоносителя (13,15 – паровоздушный молот, 41 – пневматический молот). Две последних цифры обозначают основной параметр оборудования – массу падающих частей в тоннах. Например, марка молота МА 4134 соответствует пневматическому молоту с массой падающих частей (мпч) 250 кг, а М1345 – паровоздушному молоту с мпч 3150 кг.
Гидравлические прессы
Применяются для горячей ковки заготовок, которые отличаются особо большими габаритными размерами. Например, поковку вала океанского судна куют с несколькими нагревами металла в течение суток и даже более. В молоте такая заготовка не сможет разместиться, поэтому деформацию производит ползун ковочного пресса. Такое оборудование отличается весьма большими габаритными размерами, поскольку только в таком случае можно обеспечить необходимое давление на металл.
Для механизации
Транспортных операций – подачи, кантовки заготовки в процессе ковки и т.д. – применяются специальные манипуляторы, которые могут быть безрельсового (для сравнительно небольших поковок) и рельсового типа.
Маркировка ковочных
Гидропрессов отечественного производства выполняется буквой П, после которой указываются конструктивное исполнение пресса (первые две цифры) и его номинальное усилие в тоннах (вторые две цифры). Например, марка ПБ1341 соответствует ковочному гидропрессу усилием 12500 кН.
Рисунок 3 – Ковочный гидравлический пресс с манипулятором.
Оборудование для горячей объёмной штамповки
Точность горячей штамповки должна быть по определению выше, чем ковки : во многих случаях непосредственно после деформирования деталь не нуждается в последующей доработке.
Поэтому класс горячештамповочного оборудования дополняется, кроме штамповочных молотов, ещё кузнечными бульдозерами, кривошипными горячештамповочными прессами (КГШП) и горячештамповочными автоматами. В эксплуатации продолжает оставаться некоторое количество горизонтально-ковочных машин (ГКМ).
Паровоздушные
Штамповочные молоты конструктивно отличаются от ковочных меньшими значениями энергии удара и более жёсткой конструкцией, которая связывает между собой шабот, подштамповую плиту и стойки молота (в которых перемещается баба) в единую топологическую систему.
Поскольку усилия, возникающие при штамповке, всегда больше ковочных (сказывается более сложная конфигурация штампованной поковки), то сжатый воздух как энергоноситель в данной ситуации неэффективен.
Даже при использовании мощных паровоздушных штамповочных молотов (ППШМ) по заготовке приходится наносить несколько ударов, пока она не приобретёт форму, установленную штампом. Горячая штамповка выполняется обычно с одного нагрева, поэтому скорость деформирования имеет очень большое значение. Поэтому все ППШМ — молоты двойного действия, в которых баба дополнительно разгоняется основным энергоносителем. Фото общего вида ППШМ с сомкнутым штампом представлено на рис. 4.
Рисунок 4 – Паровоздушный штамповочный молот.
ППШМ
Простые с конструктивной точки зрения машины, но надлежащую точность горячей объёмной штамповки они не всегда обеспечивают. Причины:
- Вибрация элементов оборудования и штампа;
- Остывание поковки при многократных ударах бабы молота;
- Износ рабочих элементов гравюры штампа.
Кроме того, автоматизировать штамповку на молоте в большинстве случаев невозможно. Поэтому для точной штамповки процесс проектируют на КГШП, а снижение энергии деформирования (КГШП формоизменяют металл с гораздо более низкими скоростями) компенсируют увеличением позиций штамповки.
Виду этого штампы на КГШП – составные (а не цельные, как на молотах), и представляют собой совокупность отдельных вставок, которые располагаются в последовательности, соответствующей стадиям деформирования заготовки. Это облегчает переналадку штампа, оптимизирует время вспомогательных операций и снижает вибрации при работе оборудования.
Фото общего вида современного КГШП представлено на рис. 5.
Рисунок 5 – КГШП номинальным усилием 165 МН.
Маркировка
Такого оборудования отечественного производства также представляет собой комбинированное буквенно-цифровое обозначение: первой идёт буква К, последующие две первых цифры (80 или 85) указывают на конструктивные особенность машины, а две последних – на её номинальное усилие. Например, КГШП модели КБ8544 обладает номинальным усилием 25 МН.
В условиях массового производства
Мелких и средних поковок типа толкателей клапанов, железнодорожных костылей, крупных метизов экономически целесообразно применять горячештамповочные автоматы (ГША).
В отличие от ГКМ
Эти машины имеют встроенный механизм перемещения полуфабриката от одной позиции к другой, включают в себя узлы автоматической подачи и удаления отштампованных изделий, а также оснащаются встроенными электронагревательными установками (см. рис. 6). Мировыми лидерами в производстве такого КШО являются фирмы Hatebur (Швейцария), Malmedie (Бельгия-Нидерланды) и Peltzer (Германия).
Рисунок 6 – Общий вид горячештамповочного комплекса на базе ГША модели АМР-70.
Свою нишу в производстве поковок методом горячей объёмной штамповки достойно заполняют винтовые прессы с дугостаторным приводом (см. рис. 7).
Эти машины сочетают в себе принципы статического и динамического деформирования, поскольку работают со скоростями ниже, чем молоты, но выше, чем КГШП. Штамповка происходит перемещающимся внгих винтом, который получает движение от гайки, раскручиваемой специализированным дугостаторным двигателем с бегущим электромагнитным полем.
Винтовые прессы
Применяются для производства поковок из алюминиевых сплавов, мелких и средних стальных поковок, изделий, которые имеют тонкие рёбра и перемычки. Из-за простоты управления, возможности автоматизации и низкой стоимости винтовые машины нашли широкое применение и в холодной штамповке.
Маркировка машин включает в себя букву Ф (первоначально источником привода винта являлись не электромагнитные силы, а силы трения от диска, фрикционно сцеплявшегося с элементами приводного вала) с последующими четырьмя цифрами (17 — тип привода: дугостаторный и – далее – две цифры, указывающие на номинальное усилие).
Например, обозначение АКФ 1730 указывает на автоматизированный комплекс на базе винтового пресса с дугостаторным приводом номинальным усилием 1 МН.
Рисунок 7 – Винтовой пресс с дугостаторным приводом усилием 1600 кН.
Кузнечные бульдозеры
(или горизонтально-гибочные машины, см. рис. 8) применяются для горячей гибки заготовок из толстой полосы.
Это — оборудование, которое отличается простотой конструкции и высокими эксплуатационными показателями. Используются кузнечные бульдозеры преимущественно в средне- и мелкосерийном производстве, поскольку не отличаются высокой производительностью.
Их маркировка
Включает в себя букву И (этот индекс присваивается всем видам КШО, которые выполняют гибку заготовок) и 4 цифры; две последние традиционно указывают на номинальное усилие оборудования. Например, И1230 – горизонтально-гибочная машина усилием 1000 кН.
Рисунок 8 – Горизонтально-гибочная машина.
Оборудование для холодной штамповки
Холодноштамповочное КШО различают по выполняемым операциям, среди которых:
- Разделительные/заготовительные.
- Штамповка листового материала.
- Штамповка из полосы или ленты.
- Формообразующие операции с листовым металлом (вытяжка, гибка).
- Холодная объёмная штамповка – выдавливание, высадка.
- Комбинированная штамповка из листа – листообрабатывающие центры.
В качестве заготовительного оборудования используются кривошипные или дисковые ножницы. Первые могут резать как сортовой, так и профильный прокат, в то время, как дисковые ножницы предназначены для роспуска только тонколистового металла в виде рулонов или широкой ленты.
Сортовые ножницы
Для резки прутка чаще встречаются в цехах горячей или холодной объёмной штамповки. Они представляют собой однокривошипные механические прессы с устройствами для подачи прутка и его удерживания во время разрезания.
Листовые ножницы
Машины горизонтального исполнения, которые оснащаются двумя шатунами, поскольку зона реза должна быть несколько больше ширины листа. Листовые ножницы могут иметь гидравлический привод, что используется в моделях, работающих с металлом толщиной более 16 мм.
Комплексы
На базе кривошипных ножниц оснащаются приводными рольгангами, поворотными столами и другими механизмами, снижающими трудоёмкость резки.
Маркировка ножниц отечественного производства начинается в буквы Н. Характерно, что последними двумя цифрами маркировки листовых ножниц обозначают не усилие, а толщину разрезаемого металла (одновременно указывается и предел прочности в МПа, для которого было рассчитано это усилие).
Например, модель Н1830 – кривошипные сортовые ножницы усилием 1000 кН, а НК3414 – листовые ножницы для резки листа толщиной до 2,5 мм. Внешний вид оборудования представлен на рис. 9, 10, 11.
Рисунок 9 – Многодисковые ножницы.
Рисунок 10 – Сортовые ножницы.
Рисунок 12 – Листовые ножницы с наклонным ножом
Листовую холодную штамповку ведут на механических или гидравлических прессах вертикального исполнения
Механические прессы различаются по следующим характеристикам
Количеству кривошипов
Один, два или четыре.
По форме станины
Открытая или закрытая.
По количеству стоек
Одна или две.
По наличию или отсутствию узлов
Автоматизации штамповки.
По количеству ползунов
Простого или двойного действия.
Для операций листовой штамповки, не требующих большого хода ползуна (пробивка, вырубка, гибка, неглубокая вытяжка) используются однокривошипные открытые прессы вертикального типа. Для глубокой вытяжки применяют прессы двойного действия.
Габаритные заготовки, деформирование которых не сопровождается большими технологическими усилиями, производят на двухкривошипных открытых прессах, а при значительных усилиях деформации применяют закрытые кривошипные прессы.
Гидравлические прессы в холодной штамповке используются реже, поскольку не отличаются высокой производительностью.
Общей тенденцией для холодноштамповочного КШО считается удобство управления оборудованием, для чего прессы часто оснащают автоматическими подачами, сбрасывателями, питателями.
Кривошипные механические прессы
Отечественного производства маркируются буквой К, а гидравлические – буквой Г. Принцип формирования остальных символов в маркировке не отличается от рассмотренного выше.
Листообрабатывающие центры
Они особенно эффективны в условиях мелкосерийного производства, когда из одного и того же листа можно штамповать (в основном, вырубкой и пробивкой) одновременно несколько различных по конфигурации деталей. Такое оборудование имеет роторное исполнение.
Типовые представители КШО для холодной листовой штамповки представлены на рис. 13, 14, 15.
КШО
Для холодной объёмной штамповки разделяют на две группы
Прессы для холодного выдавливания, а автоматы для холодной высадки.
Первую группу составляют
Вертикальные (реже – горизонтальные) прессы с механическим или гидравлическим приводом. Поскольку при холодном выдавливании требуется развивать большие технологические усилия, обеспечивая оборудованию одновременно и значительную жёсткость, то вместо традиционной кривошипной схемы в данном случае применяется схема кВ кривошипно-коленчатым механизмом.
Она даёт возможность при сравнительной компактности конструкции обеспечивать необходимые нагрузки деформирования заготовки. Такие машины маркируются обозначением К00 или К83/82 (последние две цифры, которые здесь не указаны, определяют номинальное усилие пресса).
Поскольку холодная высадка – технология, адаптированная под массовый выпуск продукции типа болтов, гаек, винтов и прочего крепежа, то реализуется она исключительно на автоматизированном оборудовании. Выпускаются отдельно автоматы для изготовления стержневых деталей, и для холодной высадки коротких изделий.
Для накатывания резьбы на полуфабрикатах
Выпускаются резьбонакатные станки. Они могут быть трёх исполнений:
Плашечного
Где резьба получается работой двух плашек – подвижной и неподвижной:
Роликового
Пригодного для накатки резьбы на изделиях без головки;
Планетарного
При котором накатка выполняется инструментом типа «ролик-сегмент».
Многие холодновысадочные автоматы снабжаются резьбонакатными головками, и могут производить полностью готовые метизы. Примеры современного оборудования, предназначенного для операций холодной объёмной штамповки показаны на рис. 16 и 17.
Примеры работы различных видов КШО можно посмотреть на многих видео YouTube .
Например, на видеоролике представлена работа паровоздушного молота с мпч 8000 кг.
Здесь:можно наглядно увидеть работу кривошипного пресса для холодной контурной гибки по задаваемой программе.
В ролике разъясняется устройство многопозиционного холодновысадочного автомата для изготовления болтов.
Рисунок 13 – Двухкривошипный пресс простого действия со станиной закрытого типа.
Рисунок 14 – Однокривошипный открытый пресс с С-образной станиной.
Рисунок 15 – Современный листообрабатывающий центр.